Опыт производства одежды для фигуры: 7 шагов к непревзойденному качеству
Глобальный аппетит к одежда для коррекции фигуры не подает признаков ослабления. Как взыскательный владелец бизнеса, вы понимаете, что создание исключительного корректирующего белья, придающего уверенность в себе и подчеркивающего естественную красоту, зависит не только от знания тенденций. Это требует глубокого понимания сложных процесс производства одежды для фигурыНачиная с момента возникновения дизайнерской концепции и заканчивая финальными этапами упаковки и доставки.
Это всеобъемлющее руководство проведет вас за кулисы, раскрывая семь важнейших этапов пути производства одежды для фигуры. Независимо от того, являетесь ли вы опытным владельцем бренда, стремящимся оптимизировать производственный цикл, или начинающим предпринимателем, желающим воплотить в жизнь свою идею создания одежды, этот инсайдерский взгляд даст вам знания, необходимые для принятия обоснованных решений и эффективного сотрудничества с производственной командой.
Этап 1: Дизайн и разработка - где инновации обретают форму
Путешествие начинается с идеи, с видения одежды для коррекции фигуры, которая отвечает конкретным потребностям и желаниям. Этот начальный этап - тонкий танец между креативностью, техническими знаниями и глубоким пониманием целевого рынка.
- Исследование рынка и анализ тенденций: Успешный дизайн корректирующей одежды начинается с понимания вашей аудитории. Каковы их потребности, предпочтения и болевые точки? Каковы последние тенденции в моде, тканях и технологиях коррекции фигуры?
- Концептуальные эскизы и дизайнерское вдохновение: Первоначальные дизайнерские концепции воплощаются в жизнь с помощью эскизов, досок настроения и вдохновения, почерпнутого из различных источников, включая тенденции нижнего белья, исторические корсеты и инновационные разработки в области текстиля.
- Технический дизайн и создание выкройки: На этом этапе творческое видение превращается в осязаемые чертежи для производства. Опытные лекальщики воплощают концепцию дизайна в подробные выкройки, тщательно продумывая конструкцию одежды, свойства ткани и желаемые эффекты формообразования.
- Разработка прототипа и тестирование на облегание: Прототипы, первые физические воплощения дизайна, создаются по исходным лекалам. Эти прототипы проходят тщательное тестирование на живых моделях с различными формами тела, чтобы обеспечить оптимальную посадку, комфорт и функциональность.
- Уточнение дизайна и корректировка выкройки: Результаты тестирования тщательно анализируются и вносятся необходимые коррективы в дизайн, лекала и выбор материалов. Этот итеративный процесс гарантирует, что конечный продукт отвечает самым высоким стандартам посадки, комфорта и производительности.
Этап 2: Выбор материала - основа успеха
Выбор материалов имеет первостепенное значение при производстве корректирующей одежды, напрямую влияя на ее комфорт, функциональность и долговечность.
- Поиск и контроль качества тканей: Как правило, производители одежды для фигуры сотрудничают с надежными поставщиками текстиля, чтобы получать высококачественные ткани, отвечающие строгим стандартам эластичности, компрессии, воздухопроницаемости и долговечности.
- Распространенные ткани для пошива одежды: Популярными вариантами являются нейлон, спандекс, микрофибра и сетка, которые часто смешиваются в различных комбинациях для достижения определенных эксплуатационных характеристик.
- Производительность: На выбор ткани влияют такие факторы, как степень компрессии, целевые зоны коррекции фигуры, желаемый уровень комфорта и предполагаемое использование одежды (например, повседневная носка, особый случай).
- Устойчивость и этический подход к закупкам: Все чаще бренды отдают предпочтение экологичным и этичным материалам, таким как переработанный нейлон или органический хлопок, чтобы соответствовать ценностям потребителей и минимизировать воздействие на окружающую среду.
Этап 3: Кройка и шитье - точность в каждом стежке
После утверждения окончательного дизайна и материалов процесс производства переходит на этап раскроя и пошива, где опытные специалисты превращают сырье в тщательно продуманную одежду.
- Градация и раскрой деталей: Утвержденные лекала в цифровом формате градируются на ряд размеров, чтобы соответствовать различным размерам тела. Компьютеризированные раскройные машины обеспечивают точность и минимизируют отходы ткани.
- Сборка и пошив панелей: Отдельные тканевые панели тщательно собираются и сшиваются с помощью специализированных швейных машин и технологий. Усиленные швы и тщательная отстрочка имеют решающее значение для обеспечения прочности и долговечности одежды.
- Бонитировка и опорные конструкции: Многие модели одежды для коррекции фигуры включают в себя бонитировку или другие поддерживающие элементы для усиления эффекта коррекции фигуры, обеспечения направленной компрессии или создания сглаженного силуэта. Эти элементы стратегически правильно вставляются и закрепляются в процессе пошива.
- Проверки контроля качества: На всех этапах раскроя и пошива проводится тщательный контроль качества, чтобы выявить любые дефекты строчки, выравнивания панелей или общей конструкции одежды.
Этап 4: Окрашивание и отделка - добавление цвета и функциональности
На этапе окрашивания и отделки одежда приобретает свой окончательный цвет и подвергается обработке для улучшения эксплуатационных характеристик и эстетической привлекательности.
- Методы окрашивания: Окрашивание одежды может осуществляться различными методами, включая окрашивание одежды (окрашивание готового изделия) или окрашивание деталей (окрашивание ткани перед раскроем и пошивом). Выбор метода зависит от типа ткани, желаемой интенсивности цвета и сложности дизайна.
- Финишная обработка: Для улучшения функциональности и эстетики одежды можно применить различные виды отделки. Это может быть влагоотводящая обработка для воздухопроницаемости, антистатическая отделка для предотвращения прилипания или силиконовые захваты для удержания одежды на месте.
- Совпадение и согласованность цветов: Сохранение однородности цветов в разных сериях очень важно, особенно для брендов со специфическими фирменными цветами. Для обеспечения единообразия используются строгие протоколы согласования цветов и меры контроля качества.
Этап 5: Маркировка и упаковка - последние штрихи
Этап маркировки и упаковки - последний шаг перед тем, как одежда для коррекции фигуры будет готова к продаже. Этот этап имеет решающее значение для идентификации бренда, информации о продукте и обеспечения того, чтобы одежда дошла до потребителя в первозданном виде.
- Требования и правила маркировки: Одежда для коррекции фигуры должна соответствовать правилам маркировки на целевом рынке, которые часто диктуют используемый язык, необходимую информацию (например, содержание волокон, инструкции по уходу, страна происхождения) и расположение этикетки.
- Брендинг и дизайн упаковки: Дизайн упаковки, включая бирки, этикетки и мешки для одежды, играет важную роль в идентификации бренда и передаче ценности продукта. Высококачественные упаковочные материалы и привлекательный дизайн повышают воспринимаемую ценность продукта.
- Контроль качества и инспекция: Перед упаковкой каждый предмет одежды проходит окончательный контроль качества, чтобы убедиться, что он соответствует всем стандартам по конструкции, цвету, маркировке и общему внешнему виду.
Этап 6: Обеспечение качества - поддержание совершенства от начала до конца
Обеспечение качества - это не отдельный этап, а непрерывный процесс, вплетенный в каждый шаг производства корректирующей одежды.
- Поточные инспекции: На протяжении всего производственного процесса обученные инспекторы по контролю качества проводят регулярные проверки на линии, чтобы выявить и устранить любые дефекты или отклонения от стандартов качества.
- Лабораторные испытания: Ткани и готовые изделия могут подвергаться лабораторным испытаниям для оценки их эксплуатационных характеристик, таких как эластичность, компрессия, цветостойкость и устойчивость к пиллингу.
- Аудиты соответствия: Регулярные аудиты гарантируют, что производственные мощности и процессы соответствуют передовому опыту, этическим стандартам поиска поставщиков и всем соответствующим нормам безопасности.
Этап 7: Доставка и логистика - выполнение обещаний
На заключительном этапе производства корректирующей одежды тщательно координируется доставка и логистика, чтобы обеспечить своевременную и экономически выгодную доставку бренду или розничному продавцу.
- Выполнение заказов и управление запасами: Эффективные процессы выполнения заказов и точные системы управления запасами имеют решающее значение для отслеживания заказов, управления уровнем запасов и обеспечения своевременной доставки.
- Способы доставки и логистические партнеры: Выбор способа доставки (например, морской или воздушный фрахт) зависит от таких факторов, как объем заказа, сроки доставки и бюджет. Для бесперебойной и своевременной транспортировки необходимы надежные логистические партнеры.
- Документация по импорту/экспорту: Для международных перевозок требуется соответствующая документация, включая коммерческие счета, упаковочные листы, коносаменты и все необходимые разрешения и сертификаты на импорт/экспорт.
Производство одежды для фигуры: Совместное путешествие к совершенству
Понимание тонкостей процесса производства корректирующей одежды позволит вам принимать взвешенные решения, эффективно общаться с партнерами-производителями и гарантировать, что концепция вашего бренда воплотится в высококачественной и востребованной одежде. Отдавая предпочтение контролю качества, этичному поиску поставщиков и ориентированному на клиента подходу на каждом этапе, вы сможете уверенно ориентироваться в мире производства корректирующей одежды и выпускать исключительную продукцию, которая придает уверенность и подчеркивает естественную красоту.
Почему стоит выбрать компанию S-SHAPER в качестве надежного партнера по производству форменной одежды?
На сайте S-SHAPERМы понимаем, что для воплощения в жизнь вашей идеи по созданию новой одежды требуется не просто производитель, а преданный партнер, который понимает ваш бренд, ваш рынок и вашу непоколебимую приверженность качеству.
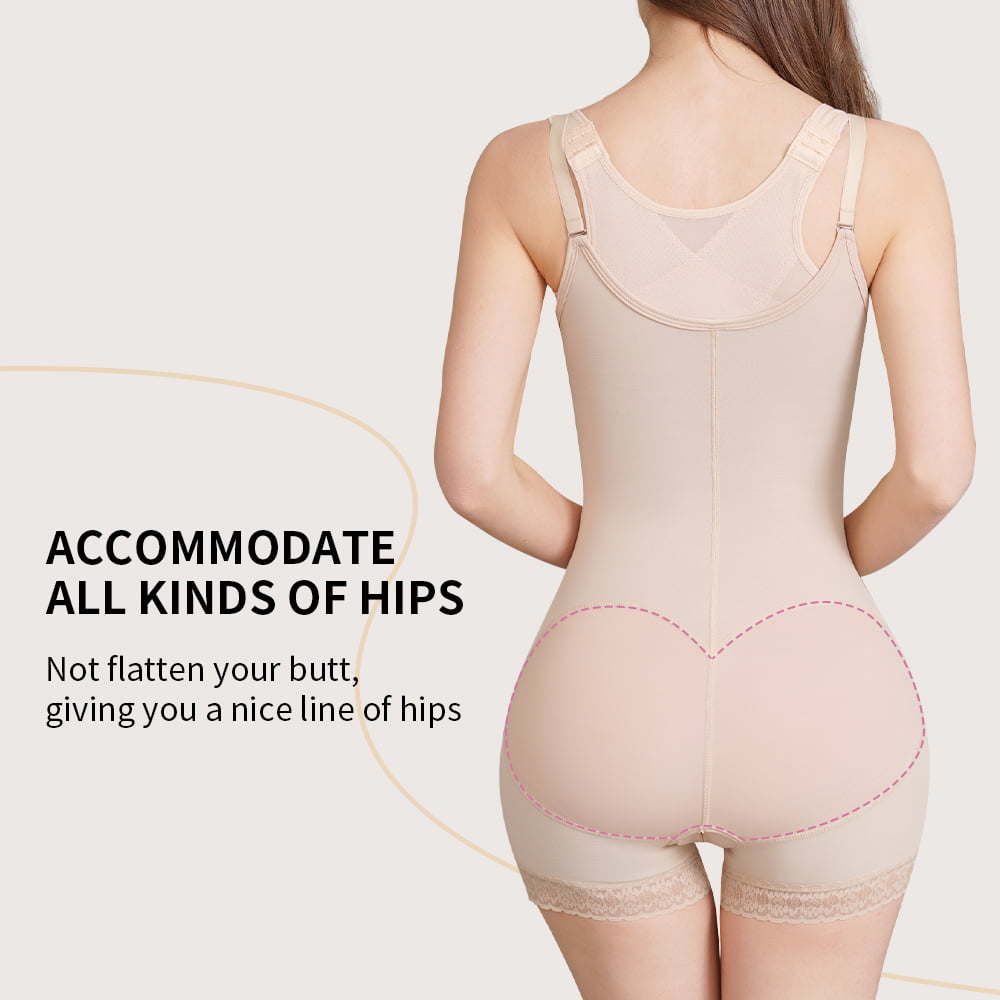

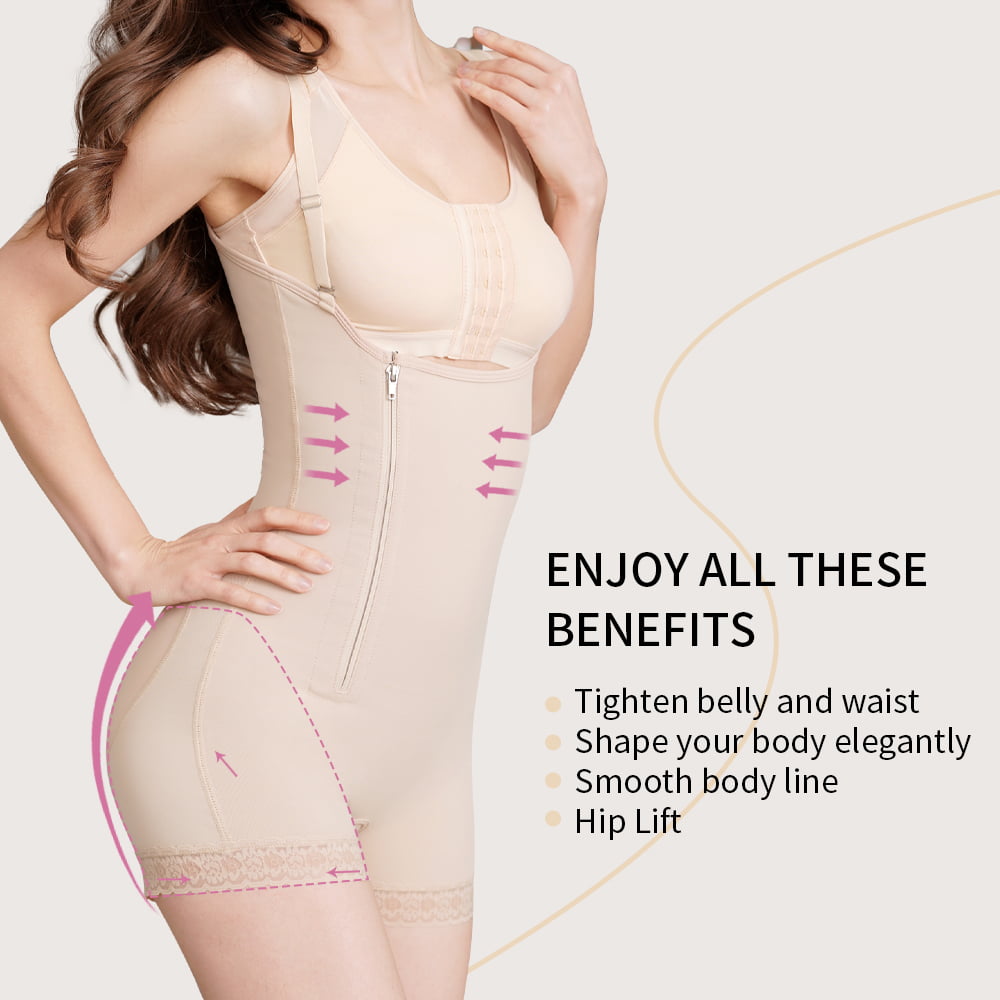
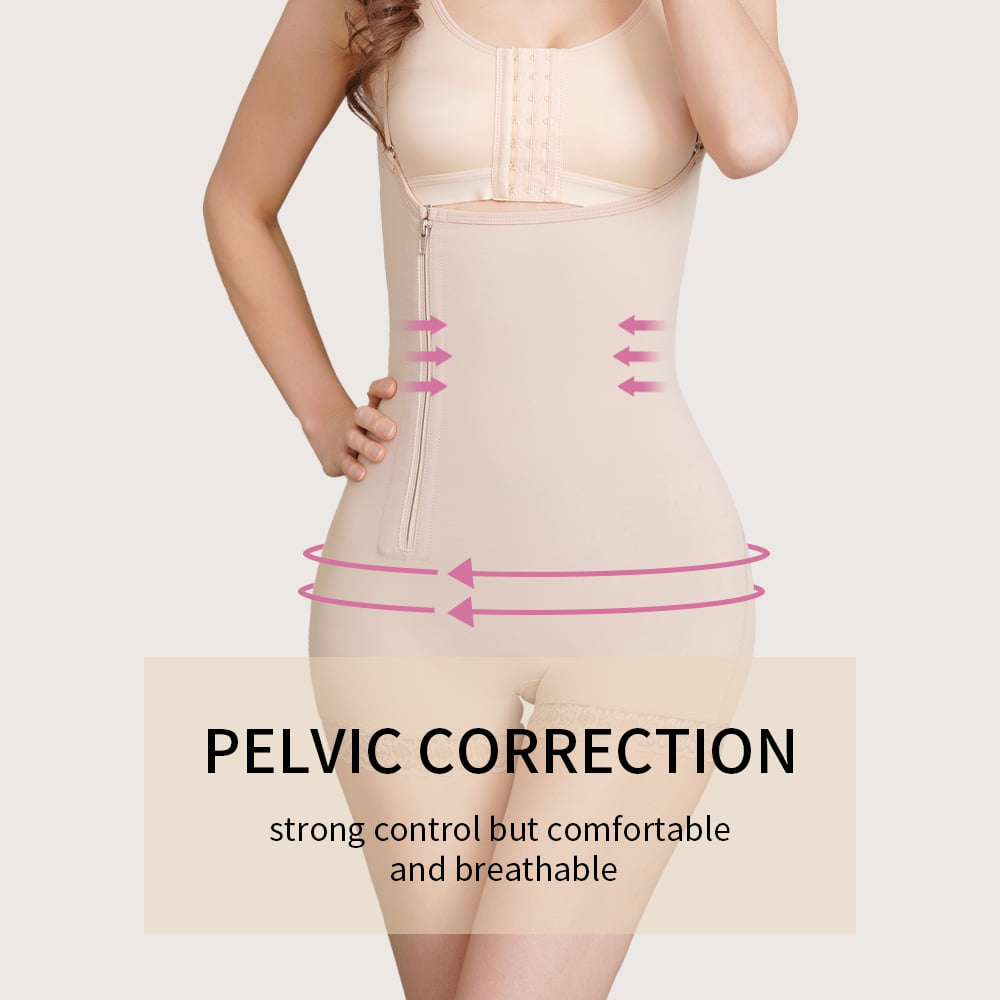
Вот как S-SHAPER превращает ваши мечты об облегающей одежде в реальность:
- Ваше видение, наш опыт: Мы сотрудничаем с вами на всех этапах - от разработки концепции дизайна и выбора материалов до упаковки и логистики, гарантируя, что ваше уникальное видение будет тщательно воплощено в жизнь.
- Персонализация - ключевой момент: Мы не верим в универсальные решения. Наши гибкие производственные возможности позволяют нам удовлетворить ваши конкретные требования, будь то мелкосерийное производство для капсульной коллекции или крупносерийное производство для удовлетворения крупносерийного спроса.
- Качество без компромиссов: Мы осуществляем строгий контроль качества на протяжении всего производственного процесса, начиная с закупки высококачественных материалов и заканчивая тщательными проверками на каждом этапе. Репутация вашего бренда - наш главный приоритет.
- Конкурентоспособные цены, исключительная ценность: Мы считаем, что исключительное качество и конкурентоспособные цены идут рука об руку. Наши эффективные производственные процессы и прочные отношения с поставщиками позволяют нам предложить вам наилучшую стоимость ваших инвестиций.
- Преданная поддержка на каждом шагу: Наша опытная и отзывчивая команда готова помочь вам на каждом этапе производства корректирующей одежды, обеспечивая индивидуальную поддержку, экспертные советы и прозрачное общение.
Сотрудничайте с S-SHAPER и почувствуйте разницу между настоящим сотрудничеством, непоколебимым качеством и страстью к инновациям, которые помогут воплотить в жизнь вашу идею создания одежды для фигуры.
Поделиться этим сообщением:
Оглавление
Самые популярные
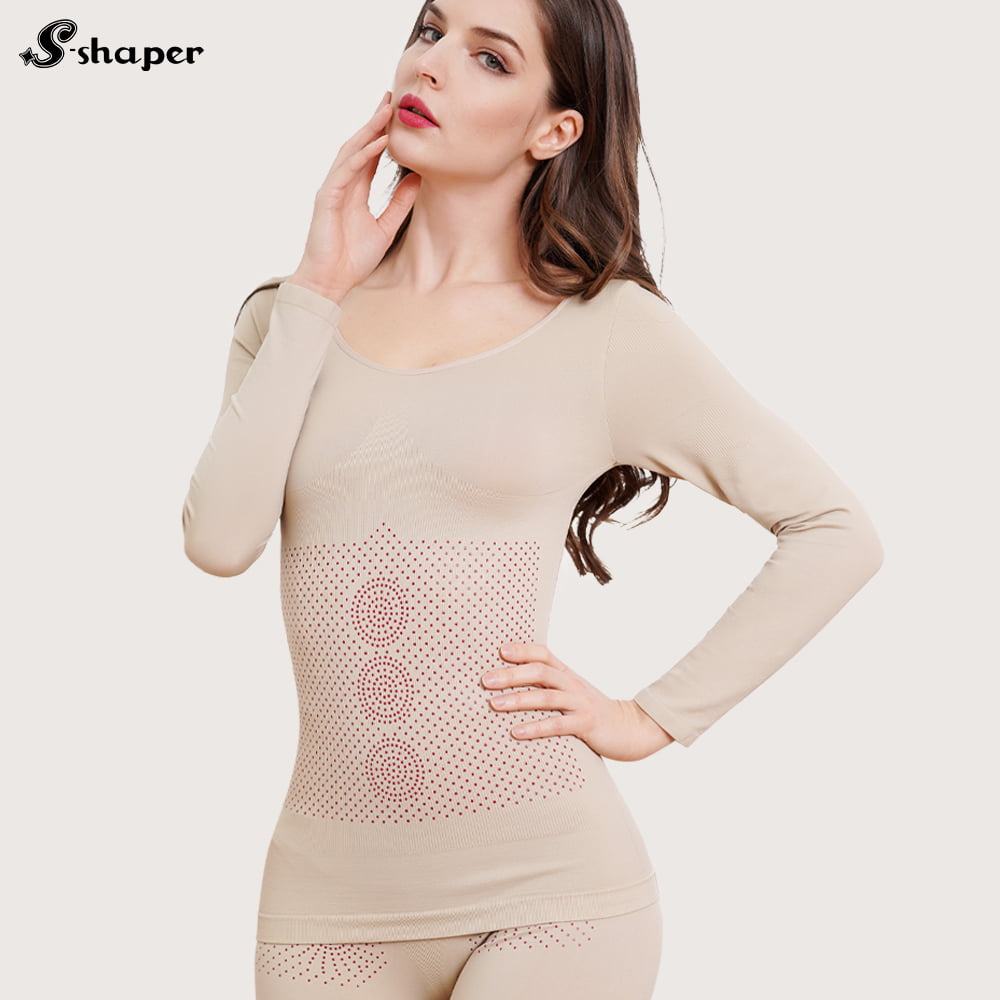
Wholesale Shapewear Dress Supplier for Instagram Brands
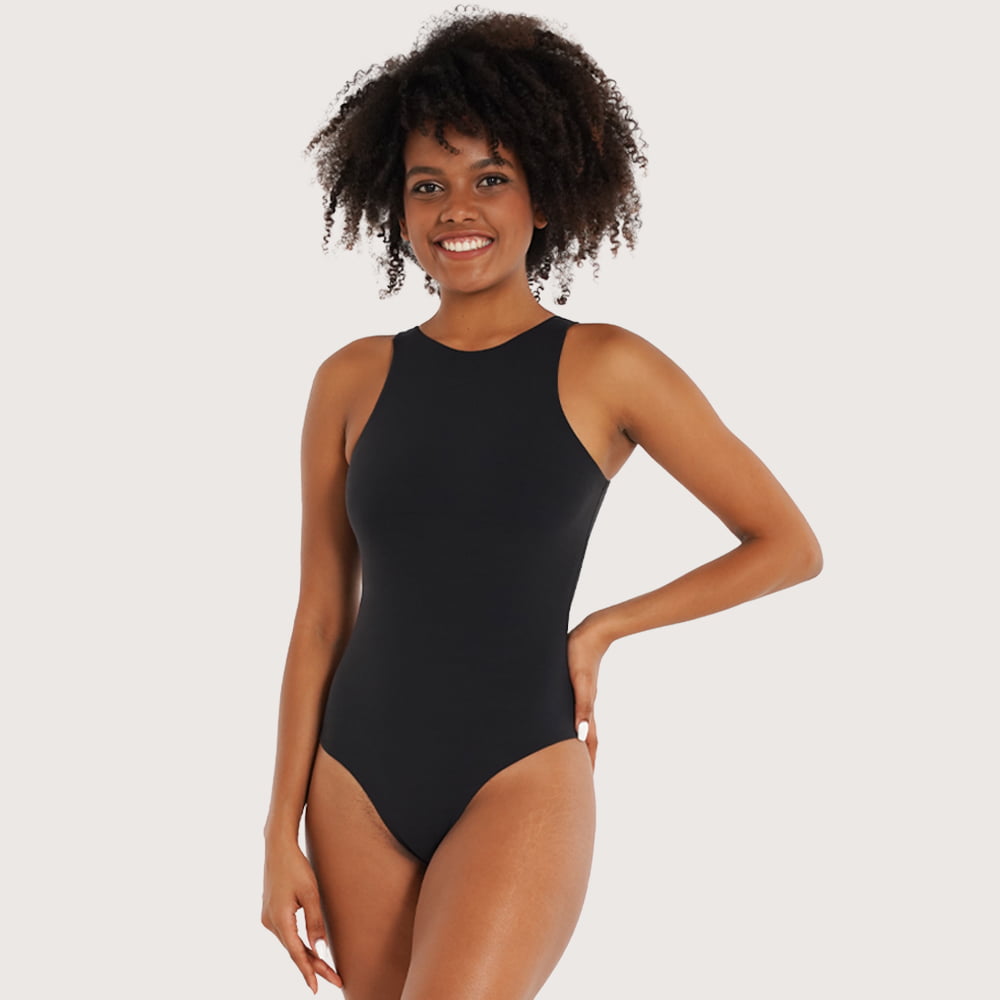
Wholesale Shapewear: Your Guide to Thriving in New Markets
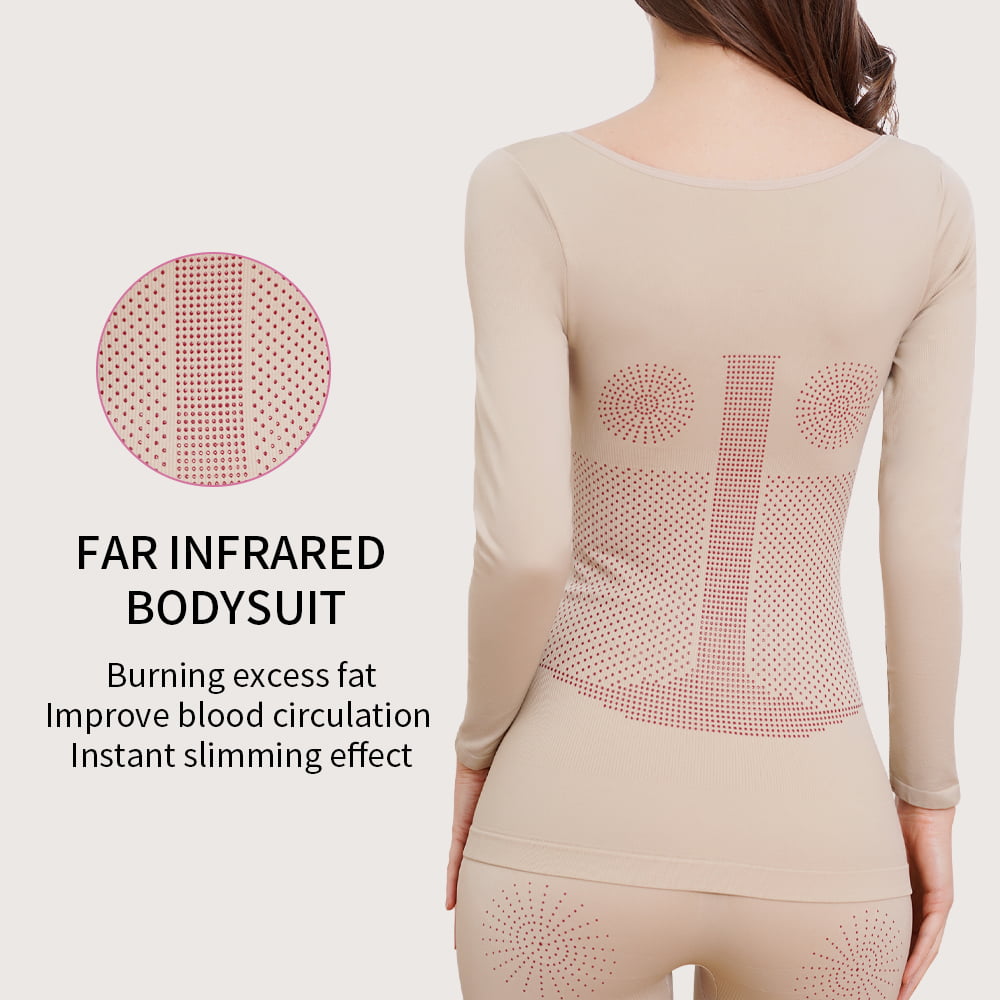
OEM Laser Cutting Panties Manufacturer for Premium Lingerie
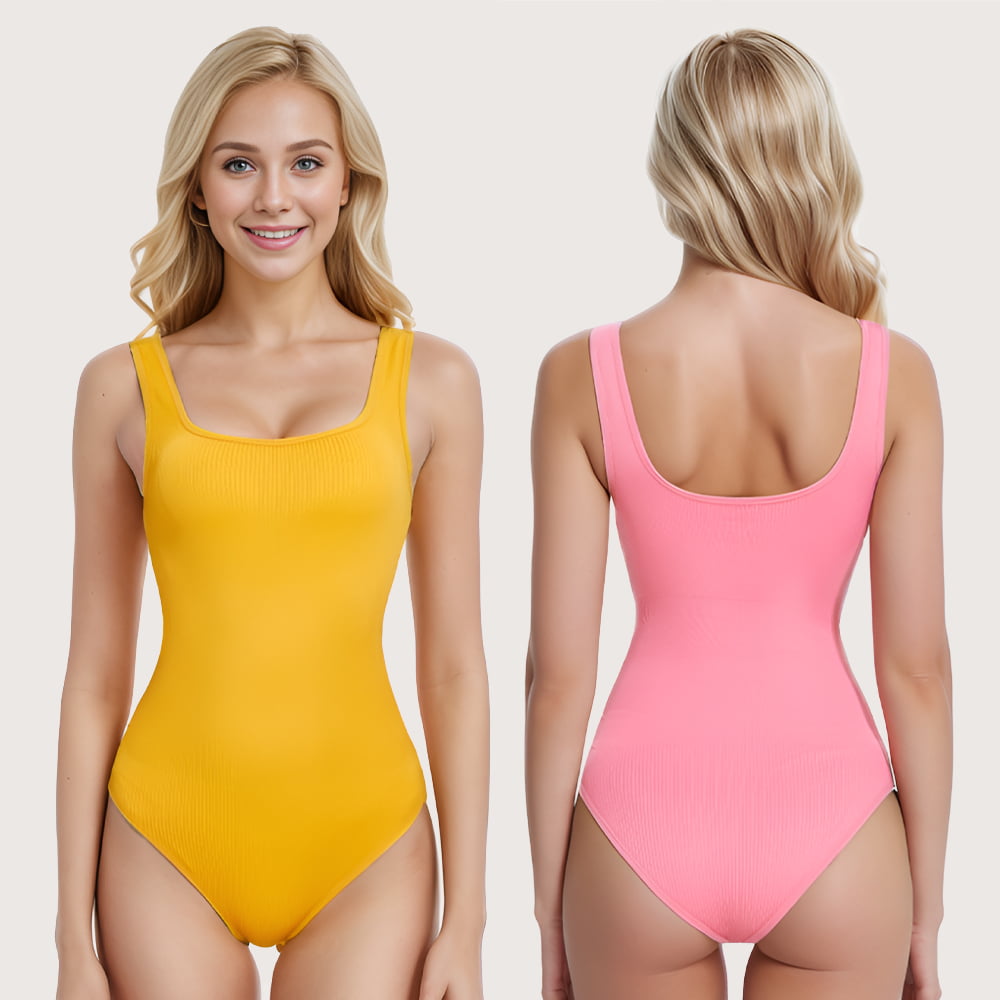
Private Label Shapewear: 7 Keys to Global Market Domination
Свяжитесь с нами
Похожие записи
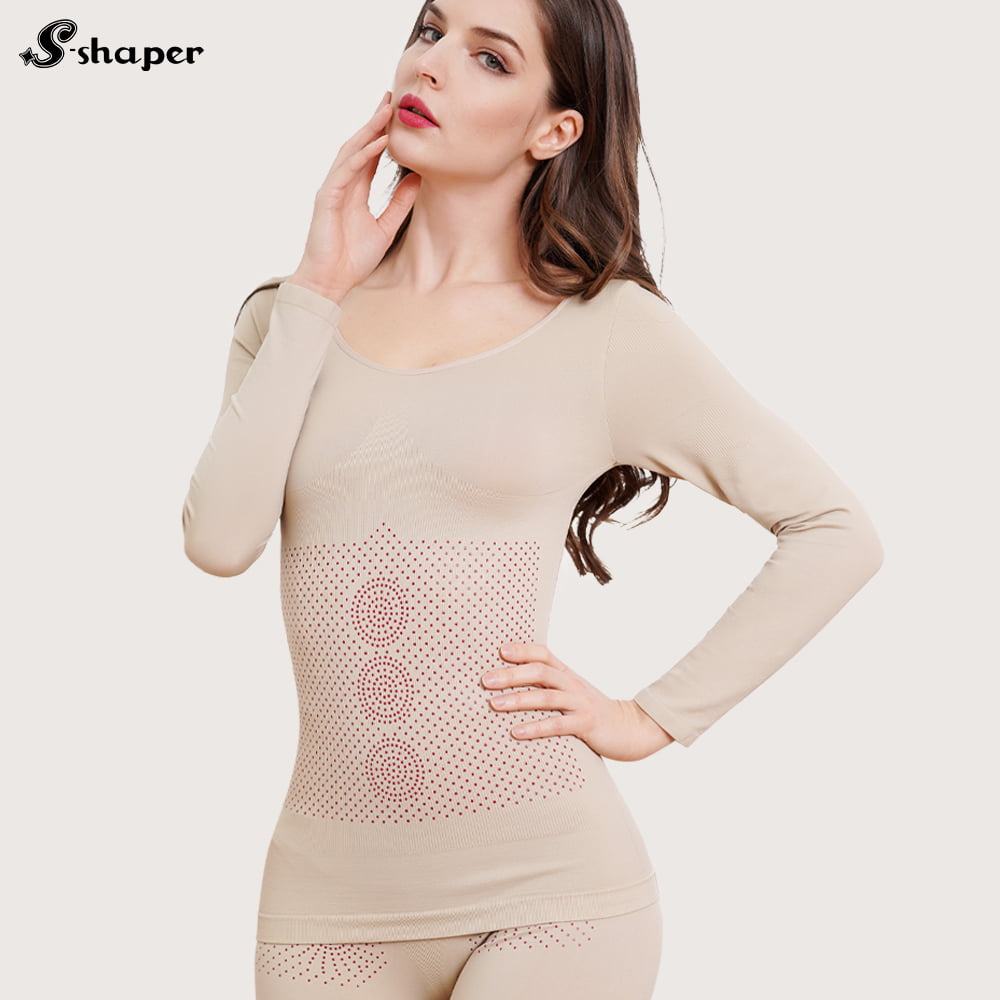
Wholesale Shapewear Dress Supplier for Instagram Brands
1. Why Shapewear Dresses Are Trending Among Instagram Fashion Brands In the age of social commerce, visual impact and product functionality are king. Instagram brands thrive on products that not
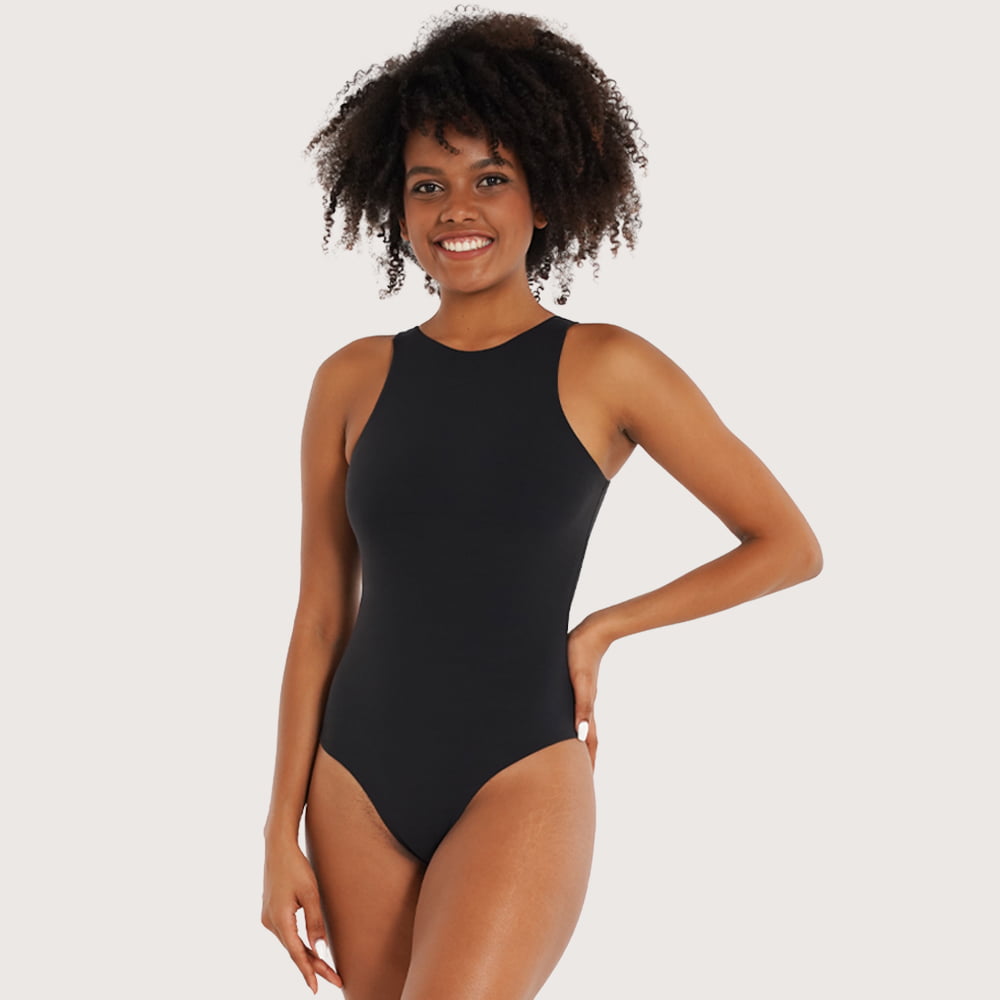
Wholesale Shapewear: Your Guide to Thriving in New Markets
The global shapewear market is undergoing a dynamic shift. While established markets like North America and Western Europe continue their steady growth, the most dramatic surge in demand—and the most
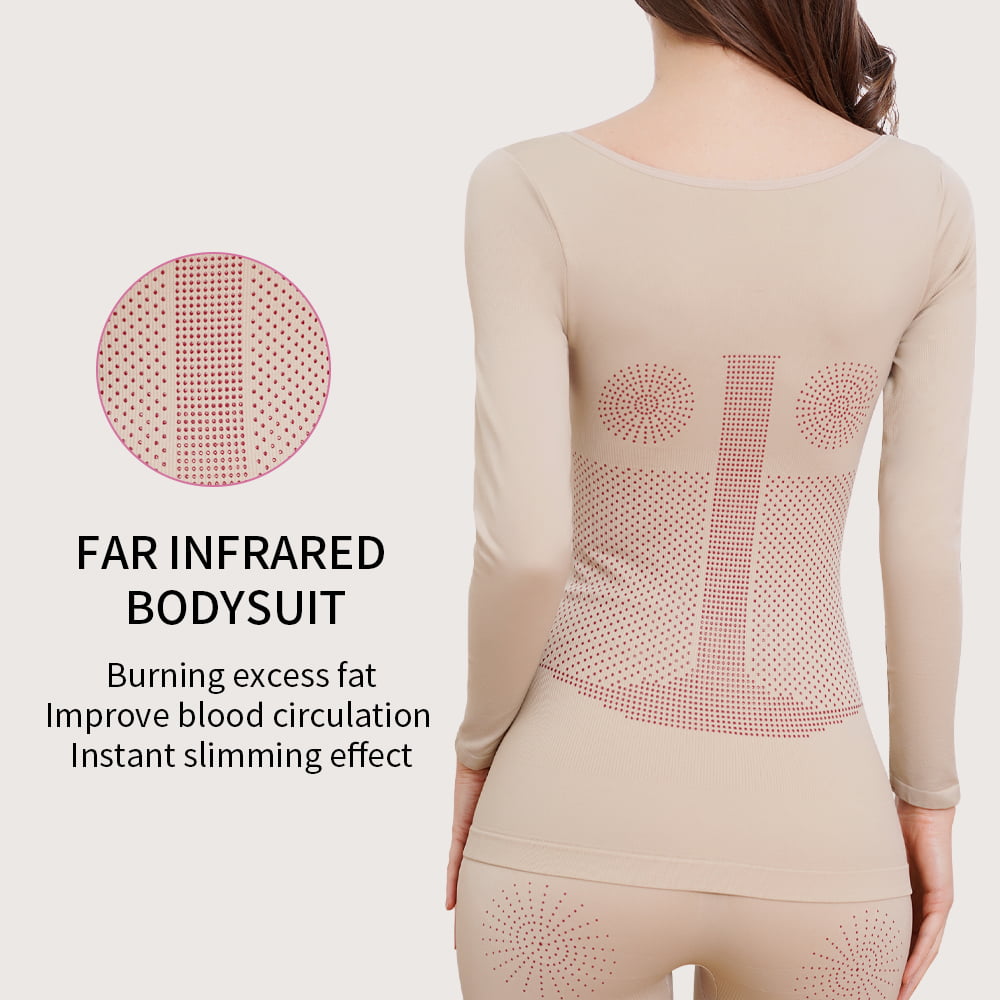
OEM Laser Cutting Panties Manufacturer for Premium Lingerie
1. Introduction to OEM Laser Cutting Panties in the Premium Lingerie Market In the evolving landscape of premium lingerie, one innovation stands out for its seamless aesthetics and high-end appeal—laser
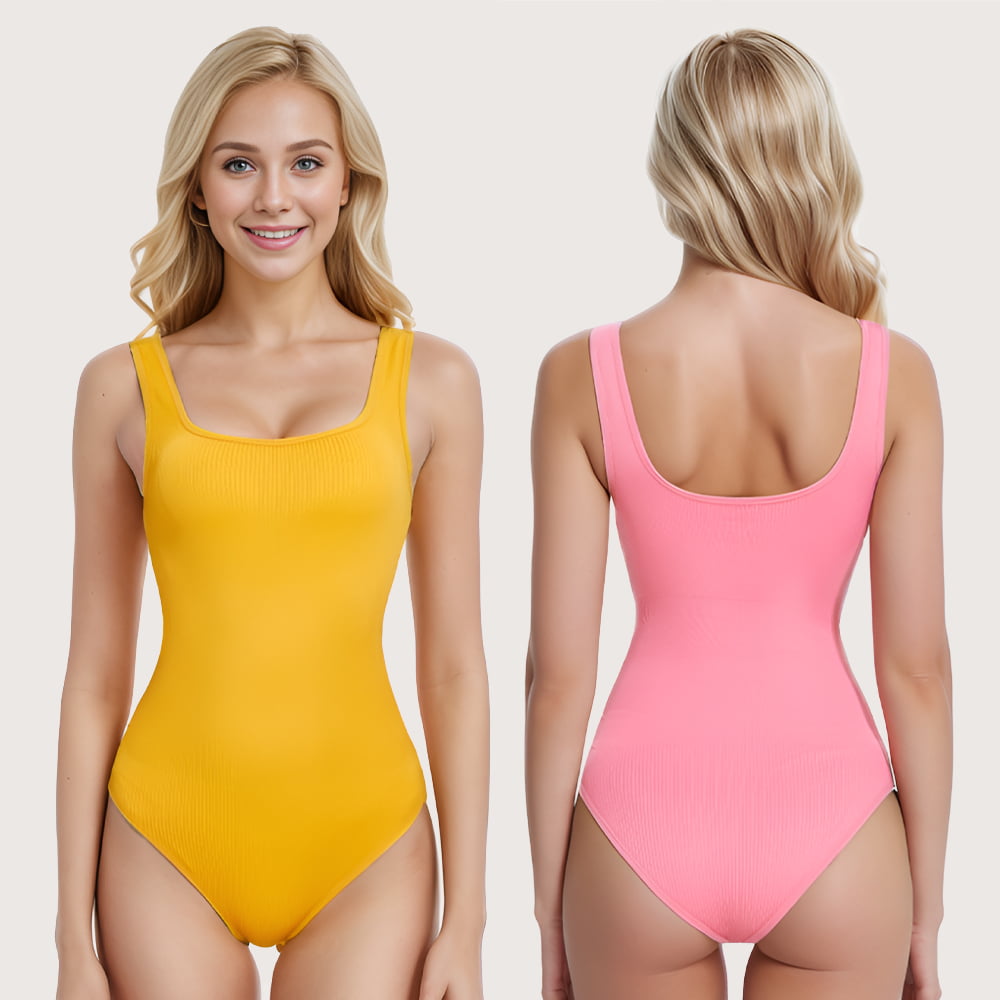
Private Label Shapewear: 7 Keys to Global Market Domination
The shapewear market is experiencing an unprecedented surge in demand, fueled by evolving perceptions of body image, a growing emphasis on self-care, and the increasing desire for comfortable yet figure-enhancing